Issue 165 January - February 2025Please note: The issue content below is just a summary of the articles in the printed magazine.
The articles are not available on-line.
Please refer to the printed magazine for the complete article.
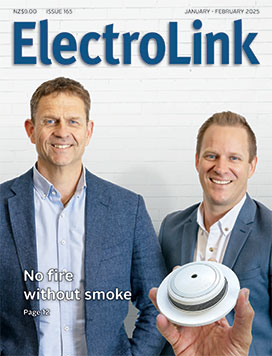
COVER STORY
Nuisance call-backs on smoke alarm installations are now a thing of the past with the launch of InTouch warranty support – the new extended support service that allows every electrician installing smoke alarms to have the supplier take care of any issue arising from their use.
InTouch is a free service available to all electricians installing CAVIUS, Watchman and SmartSense smoke alarms and is offered by their New Zealand distributor, On Point Distribution.
Managing director, Peter Smith, says he has designed InTouch to take all the risk out of smoke alarm installations for electricians by having them direct any calls from their customers to On Point Distribution who will take care of any issue like nuisance alarm callouts at no cost to the electrician or their customer.
Smith says this unmatched offer sets a new standard for support based on the quality of the smoke alarms supplied by On Point and is launched to coincide with Building Code changes that are now boosting demand for smoke alarms in new residential installations.
These changes have updated the acceptable solution for protection from fire, C/AS1, and the new edition is now being used for building consent applications submitted after 2 November, 2024.
The changes require a smoke alarm in every bedroom in a dwelling and in every living space, hallway and landing within the building and at least one on each level in a multi-level building, says Smith.
“This has increased the code requirement from one or two alarms to a home-wide system. If a kitchen or scullery can be closed off by a door, you've got to install a heat alarm and, in locations like in a garage, we also recommend heat alarms.”
Smith says these changes add substantial revenue for electrical contractors on new-builds or serious renovations and it is time for contractors who are not doing smoke alarm installations to add them in to their standard offer.
“Not only has the number of required alarms increased three-fold in a typical house, they must also be interconnected so if one alarm activates, they all sound.
Please refer to the printed magazine for the complete article
NEWS
EWRB finds electrician grossly negligent
Four and a half years after an electrical contractor replaced a rangehood in a house in Nelson, the EWRB has suspended the electrician’s licence for two years and ordered him to pay $675 in costs. The suspension was the eventual result of a disciplinary hearing conducted by the Board on 18 September, 2024. This article is based on the Board’s published 24-page decision.
The hearing was driven by a complaint laid by a government agency, WorkSafe, only days after the replacement work was carried out in February 2020. WorkSafe laid the complaint against the electrician because a man who had been hired to build a surround for the rangehood was found dead at the site. According to the EWRB, a post-mortem examination was conducted over three months later and found the cause of his death was “electrocution resulting in cardiac arrhythmia”.
The Board found that the work completed by the electrician “was not electrically safe, and, as a result, a person received a fatal electric shock”. This was assumed to have come from the metalwork of the rangehood that was livened, according to the Board, with “240 volts”.
Prior to the disciplinary hearing, the electrician had been convicted in a WorkSafe prosecution in the Nelson District Court in November 2023. The conviction from the same incident was for breaches of the Electricity Act and the Electricity (Safety) Regulations.
In its hearing, the EWRB considered the Electricity Regulations but ruled that the electrician had committed only breaches of the Act and tied this breach to the electrician’s failure to correctly test his prescribed electrical work in accordance with AS/NZS 3000:2007, which is not cited in the Act.
The Board hearing (CE No. 22287) brought by the Ministry of Business, Innovation and Employment (MBIE) against electrician Stephen Burton appears now to be the final government action against the man. Questions remain over the odd way these government actions have been carried out. No charges against Burton for causing a death were ever laid and not $1 of fines were ever awarded against him either by the court or the EWRB. The Board said in its decision that a fine was not an option that was open to the Board because he had already been convicted by a court.
The court found him guilty only of breaches of the electrical compliance regime, but he appeared to have been prosecuted by WorkSafe because of the fatal consequence of his non-compliance. Because he was not charged with causing death, he could not defend himself against that but appeared to be punished as if that was the charge.
As a first-time offender he was not jailed and was sentenced by the court to eight months home detention and ordered to pay $150,000 to the dead man’s family in reparation for emotional harm and loss. Even though the Electricity legislation provides no scope for reparations to be awarded and, despite no charges being laid under HSWA, the judge crossed over into health and safety law when it came to sentencing claiming that, “what I am required to do in a case involving matters of health and safety in a workplace is to determine first of all questions of reparation.”
Please refer to the printed magazine for the complete article
NZEIA ramps up pressure to get fit-for-purpose guidance
Poorly constructed licence changes by the EWRB combined with confusion over regulatory control of installation work has resulted in a mess that is costing New Zealand. As a direct result rapid changes are being sought by the electrical inspectors’ association, NZEIA. Vice president, Mark Harris comments.
NZEIA, the New Zealand Electrical Inspectors Association, is a relatively new organisation in the electricity industry. Our focus is on our three core principles of being competent, compliant and consistent. It goes without saying that all three include safety.
The three principles don’t just underpin NZEIA, they encapsulate the minimum requirement for all prescribed electrical work (PEW).
To further these, we produce and provide forms, test sheets, and technical guidance. Our monthly online forums help members maintain and develop their competence with recent topics including EVs, solar, hazardous areas, cable fault location and H&S management for small businesses.
During the past year NZEIA moved our focus outward, having been forced to advocate for regulatory changes.
The ‘last straw’ was the EWRB’s Gazette notice 2023 SL4075 that required electrical engineers and electrical inspectors doing PEW in hazardous areas (i.e. explosive atmospheres), mains parallel (i.e. installations exporting power) and/or cardiac protected areas to have the required endorsement(s) from 1 September 2024. However, the new and required endorsements only commence a year later on 1 September 2025.
This should have been a fast and easy fix when the issues with the Gazette notice were bought to the EWRB’s attention in 2023.
Despite NZEIA’s contact centre calls, escalation of them, calls to the EWRB’s registrar and to the presiding member, multiple items published in ElectroLink, and a meeting with the EWRB registrar, we (NZEIA and Master Electricians) have yet to see the EWRB acknowledge and address the issues raised in a competent and timely matter.
Please refer to the printed magazine for the complete article
Multiple earthed neutral 100 years on
Does a driven earth stake serve a useful purpose for installations in our MEN system of supply? Inspector Athol Gibson comments.
For 100 years we have been persuaded that using a driven earth stake in the New Zealand TN-C-S system of supply is a great idea. It has also been believed that it is essential for the safe operation of the New Zealand power supply. It is also a very well-established fact that the network companies strongly promoted that the driven earth stake was essential for the LV system to function correctly.
Since electric vehicles have come on the market, they not only have increased the use of electricity, but they have created what can be a dangerous electrical situation which will be discussed shortly.
Another phenomenon has also presented itself and that is the introduction of photo-voltaic electricity generation for personal use and any surplus generation can be exported to the national grid.
Along with the introduction of photo-voltaic generation and electric cars, there are some disturbingly dangerous side issues that have arisen. These not only need addressing, but there needs to be some urgency attached to the problem.
With a little ingenuity there are arising many ideas of what a vehicle battery can be used for and what could be run off the stored electrical energy of that battery. It is easy to conjure up suggested possibilities to use the stored energy, but in reality, there are many technical issues that come into play from a safety aspect that have to be managed.
With the existing MEN system connected to ground by a driven earth electrode, a significant situation is created. It is a very real hazard, and it has already been identified with our system in New Zealand. The hazard is that should the supply neutral break or become disconnected, whatever is connected at that time will have a voltage of some degree via the main earth conductor connected through the MEN link.
Please refer to the printed magazine for the complete article
Single or three-phase charging?
Three-phase AC charging can result in poor electric vehicle infrastructure in many real-world situations. Glenn Inkster explains how matching the charging speed to how EVs are used will optimise charging speeds better than a misplaced reliance on a three-phase supply to each charging station.
We have to fill up quickly with petrol because we don’t have the convenience of filling up at home. Applying petrol habits to EVs often has people asking for the ‘fastest’ charging available – applying standard electrical logic would be that the more kW (and phases) the faster the charging, but this is often not the case with EV charging. In addition, most of the time when people are asking for ‘fast’ they are actually wanting convenient charging – fast and convenient charging are not always the same thing.
It is easy to understand that installing a three-phase 32 amp socket outlet in a kitchen will not enable the end user to toast bread faster … changing to a larger capacity three-phase socket outlet would not change how much current (power) the toaster uses. The same is true when using ‘AC’ charging to charge an EV. An AC charging station is better described as a controlled safety switch, and having a ‘kW’ rating is confusing.
Take a look at the label on any AC charging station and even though the sales brochure may list 7.4 kW / 11 kw / 22 kW, the electrical properties on the label will always state the amps that the AC charging station (controlled safety switch) is rated for – just like any other switch or socket outlet.
The difference between an AC charging station and a standard electrical socket outlet is that there is a communication between the charging station and the car which enables the current to be reduced (if needed) from the maximum that the car’s onboard charger could use. An example of this is when a car that could use 32 amps single phase is plugged into a standard domestic socket outlet with a ‘portable charger’ that comes with the car.
Please refer to the printed magazine for the complete article
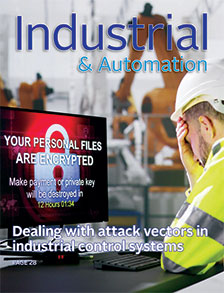
COVER STORY
Dealing with attack vectors in industrial control systems
The issue of cybersecurity remains one of the hottest topics in industry today. There are several reasons for this, not the least of which are the costs to company reputation, worker morale and financial outlay, that a cyber-based attack can bring.
Cyber safety has been discussed many times in this column but, as both the costs and rate of incidences of cyber attacks are ever increasing, it seems timely to re-visit the issue. And because perpetrators won’t stop their attacks, cyber security needs to be treated as an ongoing concern; a race that has no finish line!
This article is the first of a two-part series on cyber security, where we focus on two ‘attack vectors’ within industrial networking. The second part will discuss methods of securing industrial systems against cyber attacks. We must stress though that what we discuss here is very general in nature and the limited space available means we cannot delve too deeply into the topics covered. We therefore strongly urge both caution and continual vigilance.
The cyber landscape
Industrial security is constantly evolving and becoming ever more complex. As a science, it’s still quite immature, with the ground constantly shifting as attackers look for new angles. And while our knowledge and cyber defences have improved over the years, attacks have become progressively more sophisticated and difficult to stop.
It’s therefore important to remember that cyber risks can never be completely eliminated, as no system is 100 percent secure. The goal of any safety system is therefore to reduce risks to manageable and acceptable levels.
Why attackers attack
While the reasons for cyber attacks may seem obvious, it’s important to understand the motivation behind the actions of cyber criminals, who are also known as ‘hackers’. In doing so, we can start to comprehend what bad actors could be after, and thereby, how best to protect our systems against them.
There are many reasons hackers do what they do, the three main ones being:
- Ransomware, where attackers load a piece of ‘malware’ (malicious software) onto the victim’s system, crippling it and preventing it from being used at its full capacity. The attacker then demands payment from the victim for the restoration of their system. This is still the most common form of attack.
- Theft of trade secrets including any sensitive data that gives the victim the edge over their competitors. Manufacturers are particularly vulnerable to these types of attacks and the data stolen can include anything from formulas, recipes to customer databases.
- Express desire to cause physical damage by seizing control of operations. Public utilities and processing plants are often targeted for these sorts of attacks. Damage can range from reduced output, disabled machinery to severe consequences like power blackouts and contaminated water supplies.
Where attackers attack from
Those who seek to infiltrate an organisation have two main options, attack from the outside using cyberspace or from the inside by being physically present. We’ll now consider both types of ‘attack vectors’ and what we can do to prevent them.
Please refer to the printed magazine for the complete article
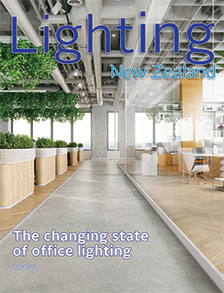
COVER STORY
The changing state of office lighting
The work office post Covid era is in a state of flux. In ushering their employees back into the office, many companies and government entities have found that widespread modifications to office expectations are creating a new dynamic in what owners, lessors, lessees and employees are demanding. The modern shift from individual offices to open plan layouts is no longer the design concept at play, instead it is trending towards flexible office spaces that incorporate everything from relaxation spaces, collaboration areas, through to café styled smoko rooms. As the office goes through this evolution, the lighting infrastructure also needs to move with the times, becoming more flexible and partial to specific space requirements.
For lighting infrastructure within the office space, there are currently several main change drivers to consider. There is the change as technology advances within the industry, the drive from clients and specifiers as they look for specific lighting parameters, and then the change driven by the morphing office styles and layouts.
Technological advances abound as suppliers try and differentiate their products from one another. The push to get clients to adopt LED luminaires is becoming a thing of the past as market saturation reaches new levels. Now it is up to suppliers to carve their product niche with pricing, refinements and product attributes.
For office luminaires the key start to the process is still pricing, with a simple split between budget conscious and specification driven, where the aim can range from being as cost-competitive as possible, to having a budget that includes upgrades from minor through to significant.
Minor upgrades from a basic luminaire can be the addition of colour or lumen select packages, the options of better diffusion or set back LED chips to create low-glare luminaires, or using higher specification hardware to improve aspects such as lumens per watt efficiency, lifespan, colour rendering and ingress protection ratings. When budget is not the major consideration, there is a raft of additional technologies that can be added to luminaires to make them more attractive for office applications.
Please refer to the printed magazine for the complete article
Lights, poles, action
An important consideration with updating exterior lighting is the poles or infrastructure they are mounted on. With new designs incorporating new luminaires and new mounting structures, these diverse elements should be duly considered by professionals within the lighting and pole installation fields.
However, as retrofit lighting installations progress, when changing the light source from traditional luminaires like metal halide or sodium lamps or upgrading LED luminaires it is also very important to ensure due diligence is taken when mounting new luminaires to existing poles or structures. Thought must be given to weight, lighting distributions, windage, chemical compositions, structural integrity of existing infrastructure and poles, as well as implications for spill light and glare when replacing existing luminaires. When a new luminaire is mounted to a fixing, the contractor is not only taking responsibility for the luminaire output, but also its integrity in staying attached.
Changing the luminaire and the impact on the light output leads to the most obvious consequences and these changes are often the reason the switch-over has been approved. The advantages, from lower maintenance costs, increased energy efficiency, higher lumen output, better light spread control and reduced glare are often key selling points for upgrading old luminaires.
However the change to LED luminaires can lead to added complications that require serious consideration before making the swap. It is generally the law of unintended consequences that create the stumbling blocks, such as altering the colour output when changing from a sodium lamp with its orange appearance to a crisp 4000 K LED floodlight, where lighting coverage can appear to shrink as the hard contrasts between light and dark create more areas of delineated shadow.
Other common mistakes can be found when installing new luminaires with distinct light output properties, such as directing an asymmetric forward throw luminaire at the same tilt angles as an existing symmetric floodlight, making for a potentially high glare and a poorly aimed floodlight effect.
Please refer to the printed magazine for the complete article
|