Issue 145 September - October 2021Please note: The issue content below is just a summary of the articles in the printed magazine.
The articles are not available on-line.
Please refer to the printed magazine for the complete article.
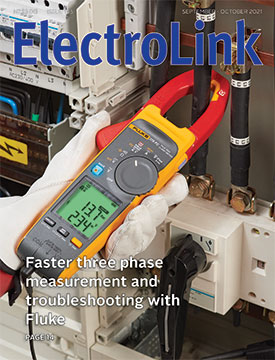
COVER STORY
Faster three phase measurement and troubleshooting
If you have ever wanted to measure voltage and current at the same time, Fluke has two new clamp meters that will test and display these results quicker and safer than ever before.
The new 377 FC and 378 FC are the first handheld clamps from Fluke to use patented FieldSense technology to measure voltage and current simultaneously within the clamp jaw, then present both amp and volt results at the same time on a dual display. Not only does this speed up and simplify testing, it is also safer because the risk of contacting live conductors is minimized with no test leads required for AC measurement.
The new non-contact, true-RMS, AC/DC clamp meters have additional features that make testing and troubleshooting a lot easier by providing more insight into what is going on in an installation. These new features include contactless three phase testing and phase rotation indication in both the new meters, with the 378 FC also offering a unique power quality function that automatically senses voltage, current and power factor issues for faster problem solving.
Using the 377 FC or 378 FC clamp tester now makes it safer to address extra-large conductors or wiring in tight spaces and more versatile for both troubleshooting and routine maintenance. The clamp jaw also makes it easier to isolate individual wires bundled in a panel and measurements can be made typically with one hand and without the risk of touching a live wire.
Fluke product engineer, Rakshita Ravi, says the speed, accuracy and safety advances the new meters add to an electrician’s productivity are further improved by the use of Fluke’s award-winning FieldSense technology that enables concurrent measurements.
Please refer to the printed magazine for the complete article
NEWS
Electrical safety upgrades for old homes
The development of a standard to improve the safety of old domestic and residential electrical installations is now back on track after a failed attempt in 2016.
A new standard is being developed to provide a defendable pathway to an installation upgrade that improves the safety of an old installation but stops short of requiring a full upgrade to the current version of AS/NZS 3000.
The first attempt by Standards New Zealand to create such an intermediate standard stumbled when a requirement for all conductors to be insulated with PVC was included in the draft.
This was interpreted as requiring VIR, TRS and old wiring to be upgraded to TPS, which defeated the purpose of why the electrical regulator commissioned the standard. The intention was to allow old cable and fittings to remain installed and to address any safety issue by maintenance rather than replacement. This would provide an approved path for failing insulation at cable terminations to be repaired with heatshrink, rather than used as a pretext to require a house to be rewired to AS/NZS 3000:2007.
The latest attempt to develop such a half-way standard to improve the safety of an existing installation, like before, is not being created as its own standard but is being incorporated into AS/NZS 3019 as a New Zealand-only provision. AS/NZS 3019 Electrical installations — Periodic verification is the standard inspectors are required to assess homeowner electrical work to in accordance with ECP 51 prior to certifying it.
Please refer to the printed magazine for the complete article
NEWS
Design and engineer licensing
There are two primary ways of regulating public safety when people carry out work: regulate who can do it to ensure they are competent, or regulate the safety outcome required and let anyone do it.
In the electrical industry where risks abound, we do both.
We draw a line where electrical work becomes too risky for unskilled people to do and recognise it as ‘prescribed electrical work’ (PEW). Then we restrict it to being carried out only by people authorised by the Electrical Workers Registration Board (EWRB) under the Electricity Act.
Then we mandate how work is to be done to manage the safety risks: we create regulations that require work to be carried out lawfully and safely; we invoke technical standards as to how to do that and we cite testing, inspecting and certification methods to verify the public will be safe. At the end of it we impose discipline and prosecution for those people that disregard the mandates.
The one area of electrical work that is not designated in the Electricity (Safety) Regulations as PEW is design. In 2006 Parliament included design as PEW in the Electricity Act but during the development of the 2010 Electricity Regulations, the government excluded design from PEW. Electricians were not required to be authorised by the EWRB to design electrical installations and electrical engineers were not required to be registered and licensed by the EWRB to carry out any electrical design work.
Up until then engineers qualified under the Engineers Registration Act or the Engineering Associates Act were allowed to do electrical design work and, despite the fact that they were not required to be registered by the EWRB, they were subject to EWRB discipline under the Electricity Act.
Please refer to the printed magazine for the complete article
NEWS
Please refer to the printed magazine for the complete article
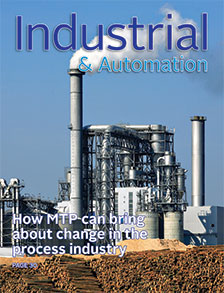
COVER STORY
How MTP can bring about change in the process industry
The process control industry typically involves larger scale production facilities which often run continuously and use a distributed control system (DCS) to handle some unique control requirements, such as the processing of a large number of analogue control loops.
A DCS typically comprises a large central supervisory control system, which provides a visual interface of the entire plant. The DCS connects to a series of decentralised (or distributed) controllers in the field, where it coordinates activities, integrating them into one homogeneous system. This process is known as ‘orchestration’, and the layer the central controller resides in is called the process orchestration layer (POL).
This control methodology has been effective in process systems for many years. The industry has however struggled adapting to change, as much of its machinery is quite large and tightly integrated. Also, those in the industry tend to be more conservative as the cost of equipment failure is high. These factors have created a reluctance to accept change.
However, modern day customer demands are markedly different to years gone by. Markets have become much more dynamic and the speed at which they change much faster. To survive, manufacturing and processing plants need to adapt to reduced batch sizes, shorter product life cycles and quicker time to market for new and updated products. Process plants can no longer operate unchanged for many years, as they have traditionally done, if they hope to keep up with consumer expectations.
So how can we overcome this? How do we make our process plants more flexible and easier to reconfigure, so that we can keep pace with customer demands that are constantly changing?
Please refer to the printed magazine for the complete article
What is IIoT and how can it help your business?
Few areas within the industrial automation space have created as much interest as the potential to improve work performance using technologies that come together in the industrial internet of things (IIoT).
Whether it is for smarter automation, remote monitoring or more reliable predictive maintenance, the connecting of devices and the ability to rapidly communicate vast amounts of sensor-driven data is enabling engineers to manage plant more effectively than ever before.
Detecting variations in measurables such as flow, vibration, temperature and volume can be automated and analysed faster and more accurately than traditional people-reliant processes. Insights gained can be sent immediately to the right people in a plant or servicing it to act on quicker.
As a result, unprecedented production efficiencies can be gained along with improvements to worker productivity and safety. The more challenging or remote the environment, the greater these gains can be.
While there is no doubting the advances the implementation of an IIOT solution can provide, developing and deploying it is a multi-discipline, plant-wide exercise that can be quite challenging.
These challenges include resolving the interoperability of different elements in the system to get everything working together, ensuring the solution and the IP-based network infrastructure is reliable, and applying more comprehensive security to manage a greater number of people accessing the system internally and remotely.
Please refer to the printed magazine for the complete article
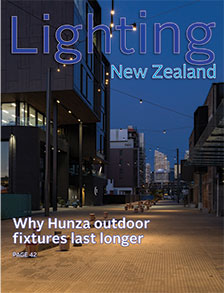
COVER STORY
Why Hunza outdoor fixtures last longer
With a simple goal of making the finest outdoor lights in the world, a Kiwi lighting manufacturer has gone a long way to achieving that with ninety percent of its sales coming from satisfied overseas customers.
From Doha to Disneyland, Hunza Lighting products are performing in outdoor settings in all climates and much of this success has come from the development work carried out in New Zealand to withstand our coastal weather.
The land of the long white salt-laden cloud has been a good proving ground for the quality outdoor fittings designed and manufactured by Hunza in Auckland, with many local architects and lighting designers specifying Hunza knowing their outdoor luminaires will last forever.
Milled and lathed by CNC machines from solid bars and blocks of natural copper, 316 stainless steel and machine-grade alloys, Hunza luminaires are weatherproof in any climates, says director Gabrielle Peace.
“Our lights are perfect for remote locations. The accuracy of CNC machining produces solid luminaire bodies that don’t warp and compromise their watertightness. The solid metal also provides more effective heat dissipation from the LED diodes, ensuring their longevity.”
Peace says the solid copper luminaire housings are designed to patina off over the years, aging gracefully and changing their metallic hue without compromising the durability of the fittings.
Please refer to the printed magazine for the complete article
Electricians upskill in lighting online
Massey University’s Graduate Certificate in Science and Technology (Lighting) has moved online, giving electricians the chance to study, whenever and wherever suits them. Graduates are very pleased with the course, and say it’s given them the confidence to try new things, and a competitive edge when it comes to securing clients.
Wayne Pretty, CEO and founder of Pretty Sweet Lighting, set out to merge design and creativity with his technical trade knowledge, and hasn’t looked back.
“After working as a sparky for more than eight years in both New Zealand and Australia, it never felt quite right to finish an electrical project that I felt could be enhanced through lighting design.
“I was continually thinking ‘There are too many lights in this space’, or ‘It would feel more comfortable in here with warmer lighting’. I knew that my role as an electrician was a little narrow, and I saw the opportunity to expand my expertise to create lighting solutions using a more integrated approach.”
He started up the Wanaka-based company after graduating from Massey in 2015, and says his studies have had a huge impact.
“I have had so much interest in my business because of the lighting certificate. We are now one of the largest electrical companies in the region, all because we offer more than the average electrician. The kinds of architectural builds we are involved with require more than an everyday sparky to do the design justice, and this kind of hands-on stuff can’t be done on a computer,” Pretty says.
Please refer to the printed magazine for the complete article
IEC environmental standards for lighting products
As customer demand for more measurability in the environment-friendly claims of lighting manufacturers, standards organisations are stepping up with solutions.
The International Electrotechnical Commission (IEC) Geneva now has an advisory group working on environmental standardisation for lighting products. New Zealand is represented in this development and an update on this initiative was featured in a Lighting Europe ‘Brussels Direct’ industry association webinar held in June, presented by Bryan King. He is the convenor of IEC TC 34 Lighting Committee, Advisory Group 20, and the executive director of Lighting Council New Zealand.
He comments as follows:
We have all often seen bold advertising claims for ‘green’, ‘sustainable’ or ‘eco’ lamps and luminaires, without any evidence-based support. However, the era of loose and vaguely expressed environmental generalities is over, with internationally standardised data now becoming an expectation for convincingly substantiating environmental performance claims.
When developed, internationally standardised IEC guidance and methods will assist with lighting specific ways for defining, calculating and reporting of circular economy, materials efficiency, embodied and operational carbon emissions performance.
Please refer to the printed magazine for the complete article
|